张宝裕 绿色建材智能装备研究院;福建南方路面机械股份有限公司
摘要:砂石骨料建材行业目前普遍采取的是“有什么用什么”的原材料策略,通过后端配方调整来被动适应原材料的波动,这限制了生产效率和产品质量的提升。为了打破这一局限,实现行业的主动转型和升级,本文提出了一种基于需求驱动的智慧建材处理加工整体解决方案。该方案依据混合料生产所需的具体骨料特性,逆向进行破碎工艺参数的建模与优化,以实现骨料性能的定制化生产。同时,通过智能管控拌和生产线,云端同步生产数据,确保生产流程的高效运行。该方案的提出不仅为砂石骨料行业的转型升级提供了有力的技术支持,而且有助于推动建材产业向绿色、可持续、高品质的方向稳步迈进。
关键词:绿色建材,智能装备,人工智能,解决方案
1. 引言
在低碳化和高质量发展的双重驱动下,建材行业正面临着前所未有的转型升级挑战。当前,骨料的选择受限于市场供应[1],搅拌站通常只能根据市场所提供的骨料进行生产。为了满足工程所需的工作性和力学性能标准,必须对搅拌成品的质量进行检测,并且对生产配方进行频繁的适应性调整,如增加胶凝材料、添加剂等的使用量。这种额外的物料投入对经济效益和环境可持续性均产生了负面影响。此外,随着骨料供给需求波动的加剧以及配合比复杂性的日益增长[2],搅拌生产过程中对材料性能或边界条件中不可预测波动的敏感性愈发凸显。
针对上述问题,科研人员已着手从改善骨料质量与管控混凝土生产过程两大维度进行了深入探究。例如,Wang等人[3]通过分形理论和级配理论控制花岗岩骨料的加工技术,并优化混凝土的级配,实现建筑和拆除废石的再利用。Coenen M等人[4]通过深度学习技术从混凝土骨料图像中预测级配曲线以便适应性地调整混凝土的配比。Huang F等人[5]采用级配在线检测方法对圆锥破碎机进行智能控制使得其排放粒径分布更加稳定。Haist M等人[6]提出了一种计算机视觉和人工智能的方法来数字化控制混凝土在整个生产与施工过程中的质量。丁廉营等人[7]通过实时在线监测砂骨料含水率等关键参数,结合混凝土配制理论,构建了混凝土智能拌和的预警与反馈调节机制,从而优化混凝土生产质量。
然而,当前的研究在骨料生产流程与混合料配方需求之间的衔接上尚显不足。鉴于此,为打破传统的思维方式,本文提出了一种智能化的建材处理加工整体解决方案。该方案旨在将搅拌配方需求与智能破碎相结合,即通过搅拌配方智能化调控砂石骨料的产出,确保骨料质量的稳定与一致,以满足实际工程中不同级配骨料需求,进而从源头处为搅拌成品的质量提供保障,同时用数字化、智能化检测来装备的三大搅拌生产链,可很好地实现生产全过程的闭环智能化质量管理。
2. 智慧建材处理加工整体解决方案
如图1所示,该智慧建材处理加工整体解决方案以混凝土搅拌为核心,从生产混凝土建材配方的具体定制化需求[8]出发,借助智能化的检测技术以及基于深度学习的人工智能控制技术对成品砂石骨料的级配、粒型、细度模数等各方面的性能指标进行破碎工艺参数建模与优化,从而实现原生骨料与再生骨料的精细化加工,为工程搅拌提供品质卓越、性能稳定的原材料。此外,通过智能管控三大搅拌产品线来保证搅拌混凝土成品质量,形成智能化、数字化、低碳化的建材设备闭环产业链升级。
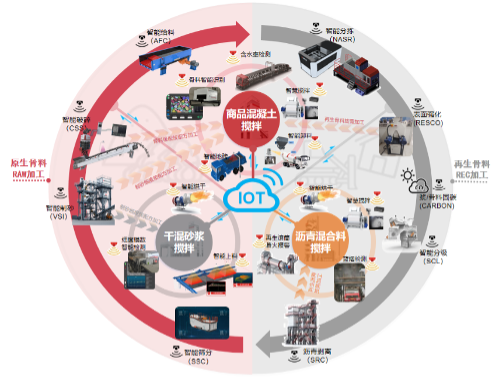
图1智慧建材处理加工整体解决方案示意图
2.1 砂石骨料按需生产
在实际投入生产之前,首先需要明确后端混合料生产所需的骨料特性,然后借助AggFlow料流产线模拟器进行破碎工艺参数的建模。在此过程中,用户将基本的进料材料和机械数据输入到工艺中,系统会自动构建出一个虚拟的料流产线模型来预测工艺的执行方式。针对每个特定的生产需求,精准地输出最佳的工艺流程,从而确保生产效率和产品质量的最大化。
在原生骨料实际生产过程中,通过智能机器视觉检测技术精确调控给料机的速度和给料量,确保骨料能够均匀、稳定地进入破碎机。随后,基于工程搅拌的生产配方需求灵活调整破碎机的运行参数,并实时监控其工作状态以进行必要的优化。应用机器视觉检测技术实时检测破碎出料,当出现破碎出料粒径偏差时,系统能够运用算法模型自动调整排料口大小以及主轴转速,以控制出料粒径,实现智能化的磨损智能补偿机制,从而确保破碎后的骨料质量稳定并满足生产需求。将破碎过程中产生的多余或不常用的石子用于精品制砂,根据生产要求以及成品砂的细度模数等调整制砂机的运行状态,提高砂子的品质。最后,配备不同类型的筛分机来满足客户的多种级配筛分需求,并对振动筛运行状态进行智能监测及故障诊断,及时发现设备异常,避免造成不可逆破坏,降低维护成本。
在再生骨料实际生产过程中,首先通过智能分拣技术进行再生骨料的回收,然后利用砂浆剥离装置有效去除骨料表面粘附的旧砂浆实现表面强化,接着再采用浆/骨料固碳技术进一步提升其性能,助力实现碳中和目标。强化后的再生骨料根据生产需求经集料分级机的分级处理与S3整形机的整形制砂,使其粒形更加圆润,级配更加合理,最后以高品质投入工程搅拌的生产过程。
2.2 三大搅拌智能管控
混凝土的生产制备过程,是在实现原材料加工的智能化调控的基础上,通过智能上料,多点布控,严格把控骨料的品质,进而对三大搅拌生产线进行智能化管理和数字化控制。
针对商品混凝土搅拌,在物料输送的皮带上安装散状物料体积流量计与含水率检测设备,用以实时检测来料的表观质量和精确的体积方量,为后续的搅拌过程提供精确的数据基础,该方案可以完美替代传统实验室抽样筛分检测级配和烘干法测量含水率,为实现全面数字化来料检测提供支持;对搅拌过程中混凝土的坍落度进行实时监测与调整,确保混凝土坍落度始终保持在预设的范围内,满足工程要求;在卸料环节,控制料斗对齐与卸料门的开口大小实现智能卸料,防止溢料撒料;最后,对施工过程中卡车卸料槽的图像进行分析,推算浆体的流速,为施工提供关键数据。
针对干混砂浆搅拌,实时检测砂的细度模数与含水率,根据不同物料的特性智能调节烘干设备的运行状态,监控烘干过程中的温度、湿度等关键参数,以优化烘干流程,去除砂中的水分,确保砂浆的质量和性能,同时大大减少因原料砂含水率波动带来不必要的能源消耗,降低吨烘干能耗,实现真正意义的节能减排。
针对沥青混合料搅拌,首先对骨料级配和含水率进行检测,然后智能调节进料速度和烘干滚筒转速烘干骨料中的水分。接着,在对废旧沥青路面材料进行再生处理的过程中,再生滚筒配备了智能视觉和温度检测装置,出现异常时能够及时报警,并且通过高温预警及高温断火检测装置实现双重保护,防止滚筒高温着火。最后,智能视觉对搅拌过程进行蓝烟与花白料的检测,有效检测与控制沥青生产过程中的污染物排放,同时确保沥青混合料的质量和施工的均匀性。
此外,控制中心能够实时监测生产数据和设备状态,确保生产流程的高效运行。所有生产信息都会实时同步至云端数据库,方便远程客户端的查询和决策。
3. 智慧建材处理加工系统介绍
在探讨了智慧建材处理加工整体解决方案的基础之上,本文将进一步以商砼生产为例,对智能骨料生产、智能商砼生产两大核心系统构成进行详细解读。
3.1 智能骨料生产系统
3.1.1 智能破碎系统
智能破碎系统依据提前设定的精细破碎工艺参数来智能操控骨料生产,并借助先进的视觉在线监测技术实时获取骨料粒径与粒形参数,实现对破碎机的智能化反馈控制。图2展示了锥形破碎机智能控制系统的构成,该系统主要包括锥形破碎机(本文以锥形破碎机为例,也可以是颚式破碎机或反击式破碎机等其他形式破碎设备)、区域扫描摄像机、传送带、LED照明装置以及边缘处理单元。
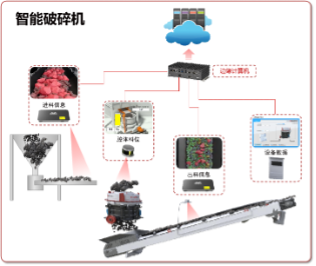
图2 圆锥破智能控制系统
在明确生产需求的基础上,系统通过实时监控上下级设备的工作状态,包括进料量、腔体料位、皮带负载等自动调整给料量和给料速度。然后,根据垂直放置在传送带上方的区域扫描摄像机和LED灯获取全站骨料图像,并采用实例分割模型对聚合图像进行准确分割,实现粗骨料分级的在线检测。最后,边缘计算机实时接收来自各个传感器和监测点的进料信息、腔体料位、设备数据和出料信息。通过对这些信息的综合分析计算大模型,系统能够全面了解破碎机的实时生产状况,包括生产电流、轴承温度以及衬板磨损情况等,从而智能地调整破碎主机的开口大小和转速等核心参数,使得骨料品质始终保持在预设的标准之内。
3.1.2 智能制砂系统
智能制砂系统主要由破碎系统、制砂智能识别系统、智能控制模型三部分组成,如图3所示,该系统通过循环优化的方式实现精品制砂过程的智能化控制。
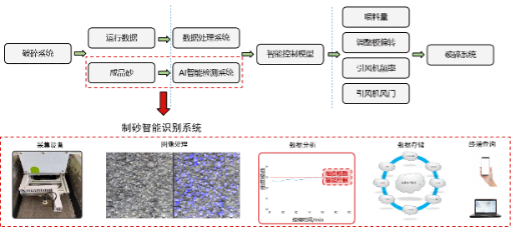
图3 制砂机智能反馈控制系统
当砂石处理系统启动时,首先会根据预设的用户需求进行初步破碎。在系统运行过程中,为了确保生产过程的监控与优化,系统会实时收集设备的运行状态信息以及成品砂的图像数据。通过AI检测技术对砂的含水率、含粉量、级配、粒形系数以及细度模数[10]进行实时在线检测,并将这些关键数据自动存储并归类,方便用户追溯查询。
在粒度控制方面,当实时检测到的粒度数据与用户预设的粒度要求存在偏差时,智能控制计算大模型系统将自动调整调整板的偏转角度,以确保获得理想的粒度分布。此外,当检测到成品砂的细度模数不符合要求或粉尘含量过高时,系统会实时调整引风机的频率和风门的开度,以优化细度模数并减少粉尘排放,确保生产过程的环保性。
3.1.3 散状物料体积流量计
散状物料体积流量计的核心部件由检测盒、电控柜及安装支架等构成,如图4所示,该设备可适用于智能破碎与智能制砂等生产线中,其主要功能是对传送带上持续移动的散状物料进行高精度的体积计量。
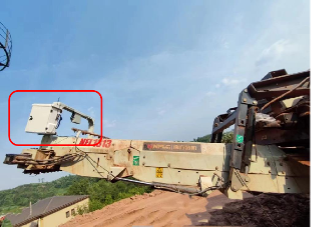
图4 散状物料体积流量计
在实际生产流程中,散状物料体积流量计采用深度相机实时获取物料图像,并将这些数据传送到工控机进行处理,借助智能图像处理技术精确地测量物料的横剖面以及传送带的进给速度,从而计算出物料的体积流量,并通过堆积密度因子将其转换为吨位,实现掌上产量监管,方便生产管理人员随时了解生产线的状态。同时,工控机中的控制算法会根据预设的配料体积比,智能地调控皮带机的启动时间和物料输送量,实现定时启动和定量输送等自动化操作。
3.2 智能商砼生产系统
智能商砼生产系统的核心组成部分包括含水率检测系统、坍落度检测系统、智能卸料系统、质量跟踪控制系统。在砂石骨料按需生产的基础上,通过集成多项先进技术和创新策略实现混凝土生产全链条的智能化监控与管理。
3.2.1 含水率检测系统
含水率检测系统主要由五大模块构成,分别是来料检测模块、料源识别模块、微波测量模块、数据处理单元、显示终端。如图5所示,该系统通过微波透射技术实时检测细集料的整体水分变化,从而监控每锅混凝土机制砂的平均含水率。
图5 微波投射测量含水率
在含水率检测系统中,各模块协同工作,确保对细集料含水率的精确检测。首先,来料检测模块会甄别传送的物料,确认其是否为细集料。随后,料源识别模块会对传输过程中的细集料进行图像采集,并从中提取与细集料种类识别相关的图像信息。紧接着,微波测量模块向细集料发射多频段的频谱信号,并捕捉这些信号穿透细集料后的衰减情况,从而获取计算细集料含水率的关键数据。数据处理单元则利用这些图像信息识别细集料的料源种类,并选取对应的微波水分模型,根据收集的数据计算出相应细集料的含水率,最后,将含水率结果传送到显示终端,供操作人员及时查看,以便同步调整骨料用量和水的用量补偿,从而保障混凝土质量稳定。
3.2.2 坍落度检测系统
坍落度检测系统主要构成部分涵盖了LED光源、摄像头、声音采集设备(如麦克风)、主轴电流采集模块以及工业计算机。其中,LED光源提供了稳定且充足的光线,确保摄像头在各种复杂多变的环境下能实时捕捉到清晰的混凝土搅拌视频。同时,麦克风用于记录混凝土在混合搅拌时所产生的各种声响。主轴电流采集模块负责收集从原材料投入至混合完成并准备卸料这一整个阶段中的电流数据。如图6所示,在每盘订单任务生产时,获取混凝土搅拌过程中的视频数据、声音数据、电流数据以及配方数据,通过调用工业计算机中预先训练好的人工智能模型进行混凝土坍落度的实时在线检测。
图6 坍落度在线监测系统
该坍落度在线监测系统可根据每个搅拌站的生产特点,综合不同模态数据特征来判断全强度混凝土的坍落度,实现对不同生产工况的强适应性,并且易于在不同搅拌站进行模型迁移应用,实现混凝土坍落度的高效、准确预测。当实际生产过程中混凝土的坍落度偏离了预设范围时,系统会及时发出警报,并根据生产配方的不同,针对性给出每盘混凝土达到预期坍落度所需的配方调整数据。同时,每盘生产状况支持实时上传云端服务器,实现远程监控,便于中控空、实验室等多方协调沟通和搅拌站数字信息化管理。
3.2.3 智能卸料系统
智能卸料系统通过在暂存仓与卸料口位置安装高清摄像头,以实现精准的卸料操作。如图7所示,当运输卡车驶入卸料区域时,运用图像分析技术确定卡车与卸料口之间的相对位置。如果检测到卡车料斗与卸料口未准确对齐,将通过自动控制系统向卡车司机提供反馈,指导其进行必要的微调。在确认对齐无误后,利用语义分割模型得到暂存仓料面、料斗以及料斗内料面的掩膜信息,进而计算暂存仓与料斗内的混凝土流量变化曲线,然后通过预先建立的在不同混凝土塌落度下暂存仓的卸料口尺寸与暂存仓内混凝土流量变化曲线之间的对应关系对卸料口尺寸进行调整,确保混凝土在卸料过程中的均匀性和稳定性。
图7 智能卸料系统
3.2.4 质量跟踪控制系统
质量跟踪控制系统采用了两大关键措施,即出厂前的坍落度补偿和施工现场的坍落度检测,以实现混凝土出厂后的质量管理。考虑到气温、湿度和运输距离等多重因素均可导致坍落度下降。因此,在混凝土出厂前需要通过大数据对环境条件和配方因素进行深入分析,运用机器学习方法实现最佳补偿预测,并根据预测结果自动调整水灰比和外加剂用量,以确保运输过程中混凝土的流动性和可塑性。搅拌车到达施工现场后,通过其卸料口斜槽部位安装的摄像系统获取卸料图像,利用逐帧光流法推算浆体的流速,进而间接反映混凝土的性能,为施工提供关键数据,确保工程项目的长期可靠运行。
4. 总结
本文提出的智慧建材处理加工整体解决方案,通过搅拌站的配方需求逆向调整破碎工艺参数,实现了骨料产出比例的智能化调控。同时对混凝土性能进行全过程的在线智能化监控,确保了每一批混合料都能达到预设的质量标准。这种闭环的产业发展模式可以有效改善当前生产中存在的质量控制等相关问题,为工程建设提供更加稳定、高质量的骨料和混凝土建材。
未来,南方路机将继续深化环保与智能化的设计理念,不断探索新的技术路线,提升产品的智能化水平,优化生产流程,推动产品线的进一步融合与发展,为构建绿色低碳、环保可持续的工程建设体系贡献更多力量。
参考文献
- 庄淑蓉,TORRES Aurora,陈睿山,等.中国砂石资源利用的现状、问题与解决对策研究 [J]. 华东师范大学学报(自然科学版), 2022, (03): 137-147.
- Wang B, Yan L, Fu Q, et al. A Comprehensive Review on Recycled Aggregate and Recycled Aggregate Concrete[J]. Resources Conservation and Recycling, 2021, 171(5).
- Wang Q Z, Zhao Y F, Tseng M L, et al. Performance analysis and reuse of construction and demolition waste stone using fractal and gradation theory[J]. Journal of cleaner production, 2020, 271.
- Coenen M, Beyer D, Haist M. Granulometry Transformer: Image-based Granulometry of Concrete Aggregate for an automated Concrete Production Control[C]. Proceedings of the European Conference on Computing in Construction (EC3), 2023, 26.
- Fang H, Ji X, Yang J, et al. Adaptive control method and experimental study of cone crusher based on aggregate online detection[J]. Physicochemical Problems of Mineral Processing, 2024, 60(3): 188759.
- Haist M, Heipke C, Beyer D, et al. Digitization of the concrete production chain using computer vision and artificial intelligence[C], Proceedings of the 6th fib Congress, 2022, 434-443.
- 丁廉营,马明刚,严良平,等.基于全过程的混凝土生产质量智能化管控及实践[J].水力发电, 2023, 49(02): 55-62.
- Wan J, Li X, Dai H N, et al. Artificial-intelligence-driven customized manufacturing factory: key technologies, applications, and challenges[J]. Proceedings of the IEEE, 2020, 109(4): 377-398.
- 冯春花,黄益宏,崔卜文,等.建筑再生骨料强化方法研究进展 [J]. 材料导报, 2022, 36 (21): 88-95.
- Huang F, Yang J, Fang H, et al. Research on online measurement method of fineness modulus of manufactured sand based on deep learning[J].Construction & Building Materials, 2024(Feb.2):414.
相关推荐: 基于质量控制的骨料建材处理装备智能化整体解决方案张宝裕 绿色建材智能装备研究院;福建南方路面机械股份有限公司 摘要:砂石骨料建材行业目前普遍采取的是“有什么用什么”的原材料策略,通过后端配方调整来被动适应原材料的波动,这限制了生产效率和产品质量的提升。为了打破这一局限,实现行业的主动转型和升级,本文提出了一…